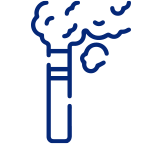
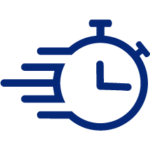
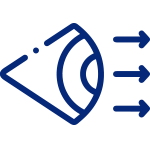
In total 6 stacks
were inspected
189 measurements were swiftly captured
Operations beyond
line of sight
Maintaining the safety and integrity of assets is a top priority in the oil and gas industry, especially in refineries where equipment is subject to harsh conditions. Ultrasonic Thickness (UT) measurements play a critical role in ensuring the integrity of assets such as furnace stacks, which are exposed to extreme temperatures, pressures, and hazardous gases. Thin metal walls caused by corrosion, erosion, or other forms of damage can compromise the safety and reliability of stacks. Therefore, accurate and timely UT measurements are essential to identify potential issues early and plan for maintenance or replacement.
In the conventional approach, rope access has been utilized to examine furnace stacks. However, this method has its limitations, including being costly, time-consuming, and potentially risky for inspectors. Additionally, considering that other activities are happening in the refinery and around the stacks, it’s important to prioritize the safety of the surroundings.
SKYRON is an intelligent flying robot that has emerged as an alternative to overcome the challenges of stacks inspections. SKYRON is equipped with advanced technology, such as a Rotary Arm, an Olympus 38DL PLUS gauge, and a digital FPV (first-person-view) system. The FPV camara provides the operators with a near zero latency HD video feed, allowing for operations beyond line of sight. With these tools, SKYRON can access furnace stacks easily and efficiently to capture accurate readings, providing valuable information about the integrity of these structures. By using this technology, inspection time and costs can be reduced, while safety and accuracy can be improved.

Recently, SKYRON was deployed to inspect six furnace stacks at a Canadian refinery. The objective was to measure the wall thickness of the outer shell of the stacks at high elevations, above the highest decks. This is a challenging task that typically requires rope access or other conventional inspection methods, which can be risky and costly. However, with SKYRON, the inspection process was streamlined, and the results were highly accurate. On average, SKYRON took only 14 minutes of flight time to inspect each stack. In the inspection of assets using SKYRON, attachment is a crucial process that involves the robot’s robotic arm locking onto the asset. This attachment enables the transducer to move within a 2” x 2” window, which allows for several UT readings to be taken at different thickness measurement locations. In total, 189 readings were taken for the six furnace stacks.
Additionally, to ensure efficient communication and report generation, the project team utilized Avesoft, our proprietary software. This software streamlines the inspection process, allowing for real-time data capture, analysis, and reporting. The use of SKYRON and Avesoft together enabled the team to gather and analyze data quickly and efficiently, saving time and resources while ensuring the accuracy and reliability of the inspection results. The innovative UT inspection technology offered by SKYRON guarantees the timely detection of potential issues with furnace stacks, allowing for necessary maintenance or replacement to be carried out promptly. As a result, there is less downtime and reduced costs associated with future complex repairs.
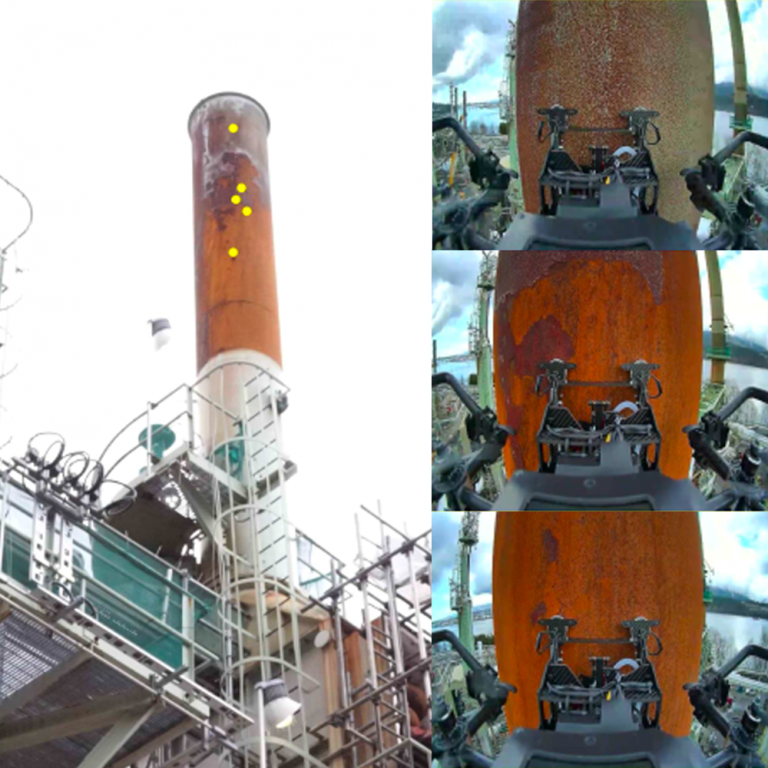
In conclusion, the use of SKYRON represents a significant advancement in furnace stack inspection technology. SKYRON’s technology provides a safer, more efficient, and cost-effective approach to maintenance and safety in refineries. With this innovation, what would typically take several days or weeks is now completed in reduced time, improving safety for inspectors and reducing downtime and repairs in the future. The application of this technology is expected to continue to expand, improving asset integrity in refineries and other industries.