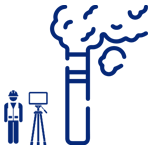
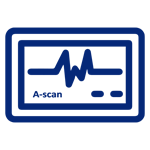
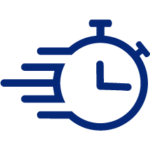
First flying robot
NON-ENTRY inspection
76 UT measurements captured
64 minutes
of flight time
In the non-destructive testing (NDT) field, experts are continuously looking to improve inspection operations to enhance efficiency, accuracy, and, above all, safety. Recently, Avestec and Acuren achieved a significant milestone by conducting the first non-entry ultrasonic testing (UT) inspection inside a confined space using an aerial robot. This successful application took place during the inspection of a stack at a refinery in Western Canada.
The interior of stacks is highly susceptible to damage. However, inspecting this area poses numerous challenges due to its confined nature. Limited access stands as a primary obstacle during these inspections, as stacks are designed with narrow passages and tight spaces that impede the entry and movement of human inspectors. These restrictions significantly restrict physical access and maneuverability within the stack’s interior.
Another challenge for interior stack inspections is limited visibility. The confined spaces lack proper lighting and have restricted visibility, making it challenging for inspectors to accurately assess the inner walls or identify potential defects. Insufficient visibility hampers the effectiveness of inspections, requiring alternative advanced methods to overcome this limitation.
Time and cost are significant factors to consider in stacks inspections. Traditional inspection methods often require extensive downtime and resources. Shutting down the stack for inspection purposes can disrupt production and lead to financial losses. Therefore, finding alternative approaches that minimize downtime and reduce costs while maintaining inspection quality is crucial.


To address the challenges associated with inspecting the interior of stacks, Avestec implemented a successful solution by conducting the first non-entry ultrasonic testing (UT) inspection using an aerial robot. This groundbreaking inspection took place inside a narrow stack that measured 50 meters in height and 4 meters in diameter. Unlike conventional methods that would have required personnel to enter the confined space, Avestec opted for a fully remote non-entry operation with SKYRON to ensure safety and overcome complexities.
During the UT inspection, the pilot and inspector operated SKYRON from a location outside the confined space. To facilitate seamless communication and data transmission, various communication links were established through a wired relay. These included flight and navigation systems, pilot TPV (Third Person View) and FPV (First Person View) for visual monitoring, inspector video feed, and inspector robotic control. By utilizing these communication links, the team was able to gather valuable data from inside the stack while ensuring the safety and efficiency of the inspection process.
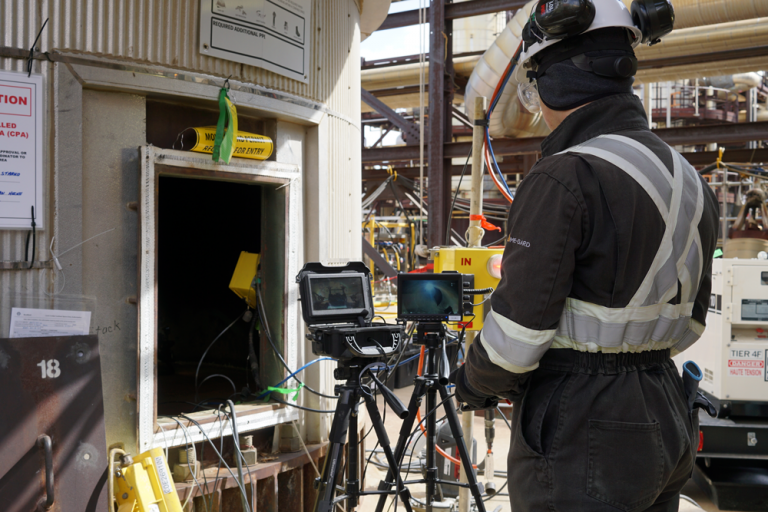
SKYRON enabled an inspections beyond the visual line of sight, ensuring a thorough examination of the confined space. One of the main features of SKYRON is its First Person View (FPV) system, equipped with a high-quality low-light camera, which provides a clear view of the inspection area. This improved visual capability allows inspectors to accurately assess the interior of the stack, identify potential problems, and evaluate its structural integrity with precision.
Another important feature of SKYRON is its magnetic attachment technology, which enables very accurate measurement of rough and rusty surfaces commonly found inside confined spaces that process chemicals or high-temperature gases. Additionally, SKYRON’s battery-less tethered power delivery system eliminates the need for battery replacement and enables long, uninterrupted flight missions inside the tank. This, in turn, facilitates a very time-efficient inspection.
SKYRON’s advanced capabilities and ability to overcome access limitations make the inspection process comprehensive and accurate.
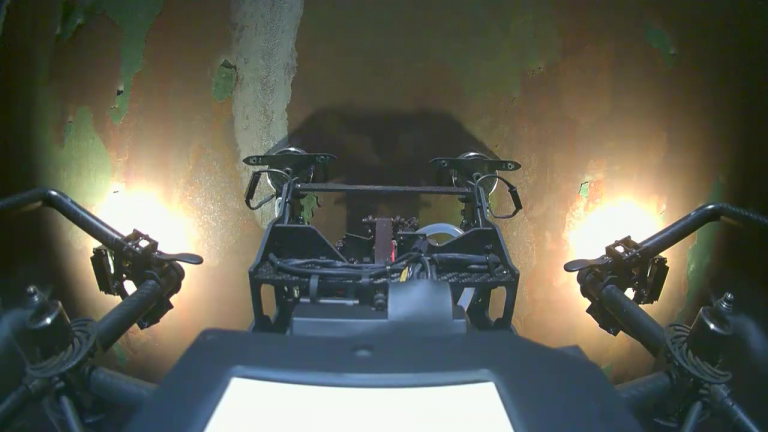
The inspection utilizing SKYRON produced outstanding outcomes. A total of 76 UT measurements were meticulously captured within 64 minutes of flight time. This remarkable efficiency and speed of data acquisition highlights the immense potential of employing aerial robots in confined-space inspections.
The application of advanced technologies has brought about a revolutionary change in the inspection of stack interiors, effectively tackling the challenges they present. Avestec’s pioneering non-entry UT inspection using SKYRON stands as a remarkable achievement for confined-space inspections. The utilization of cutting-edge robotic technology has revolutionized the way NDT professionals approach challenging inspection environments. Through the elimination of human entry and the implementation of advanced aerial robots like SKYRON, a remarkable improvement has been achieved in terms of safety, efficiency, and data accuracy showcasing the transformative power of innovative robotic solutions.